Application of RFID in the production and work of CNC machin
1. Introduction
Production enterprises are often personnel-intensive enterprises, and the management of enterprises is often more complicated. Most of these enterprises are managed through systems, and the most important point in system management is: Are there loopholes? Whether to implement In place? If not, good management results will not be achieved. Any disconnection or problem in the production link will cause disconnection or problems in the entire production chain, which will affect product quality and affect the company's brand. So how to manage each point in the production chain? Do it seriously? How to combine advanced management concepts and management methods has always been what production-oriented enterprises have been looking for.
This system is based on the actual needs of the factory, using the most advanced RFID technology (radio frequency technology), image processing technology, network communication technology, and digital processing technology combined with factory management, to manage the attendance management of factory personnel and enter the work area for management, etc. Realize intelligent control, and make the management of the factory more efficient and intelligent.
2. Program overview
Each employee distributes an electronic label badge, the label stores the designated ID number that can uniquely identify the employee, and can also store the simple information of the employee: name, title, type of work, contact information, department, etc.; other more detailed information It can be stored in the back-end database corresponding to this ID number for management personnel to query and access.
When employees enter a certain area, readers and antennas are installed at the entrance and exit of the work area to read tag information.
When the card reader reads the information, it sends the data to the upper computer of the system through the communication interface, and compares it with the employee’s information in the upper computer: if the employee’s information matches the information in the back-end database, it can be entered smoothly; Does not belong to this working area, that is, the information does not match, then the card reader will give an alarm after reading this signal (the alarm method is: 1, on the interface of the management system, prompt 2, there is a management system that controls the on-site sound and light alarm Device). Tell the management staff that the employee does not belong to this work area and is illegal entry, and corresponding measures can be taken.
Set the number of people entering each production workshop area in the background. If the authorized personnel are full, when someone enters the production workshop, the card reader reads the employee's information and gives an alarm, prompting that the number of employees has been exceeded, and the LED realistic screen sound and light alarm.
3. Overview of basic functions
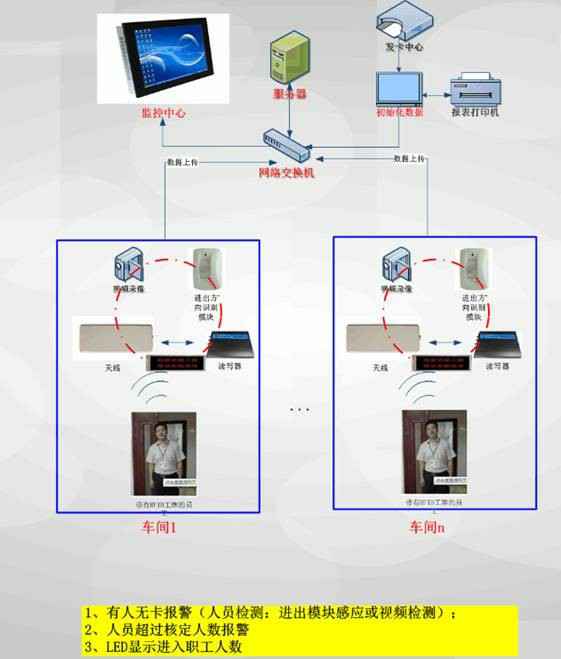
Implement unified and standardized management of the personnel involved in the system to realize the digitization and informatization of the information of the identified objects and the standardization and systematization of the overall process:
1. Real-time management, quick and easy operation, detailed log record, complete "management link";
2, automatic identification, long distance, high precision, good anti-interference, strong environmental adaptability, and realize "intelligent judgment";
3. Information is disclosed by level, with strict authority control and clear levels, to achieve "upward responsibility";
4. The system data and the system hardware fingerprint are bound and encrypted, and the module data is encrypted for transmission;
5. The system is independently encrypted and coded to prevent information leakage and facilitate data fusion;
6. Strong supervision and supervision, requiring personnel to consciously abide by system rules and operating procedures, which facilitates real-time control, inspection and supervision by leaders;
7, humanized management, avoid conflicts, unique early warning and alarm functions;
8. Unique quantitative management of safety credit value and quantitative work statistics, which is convenient for quantitative assessment;
9. Distributed structure, convenient for networking, mobile deployment and scope expansion;
10. Modular design, convenient for function expansion and special module customization